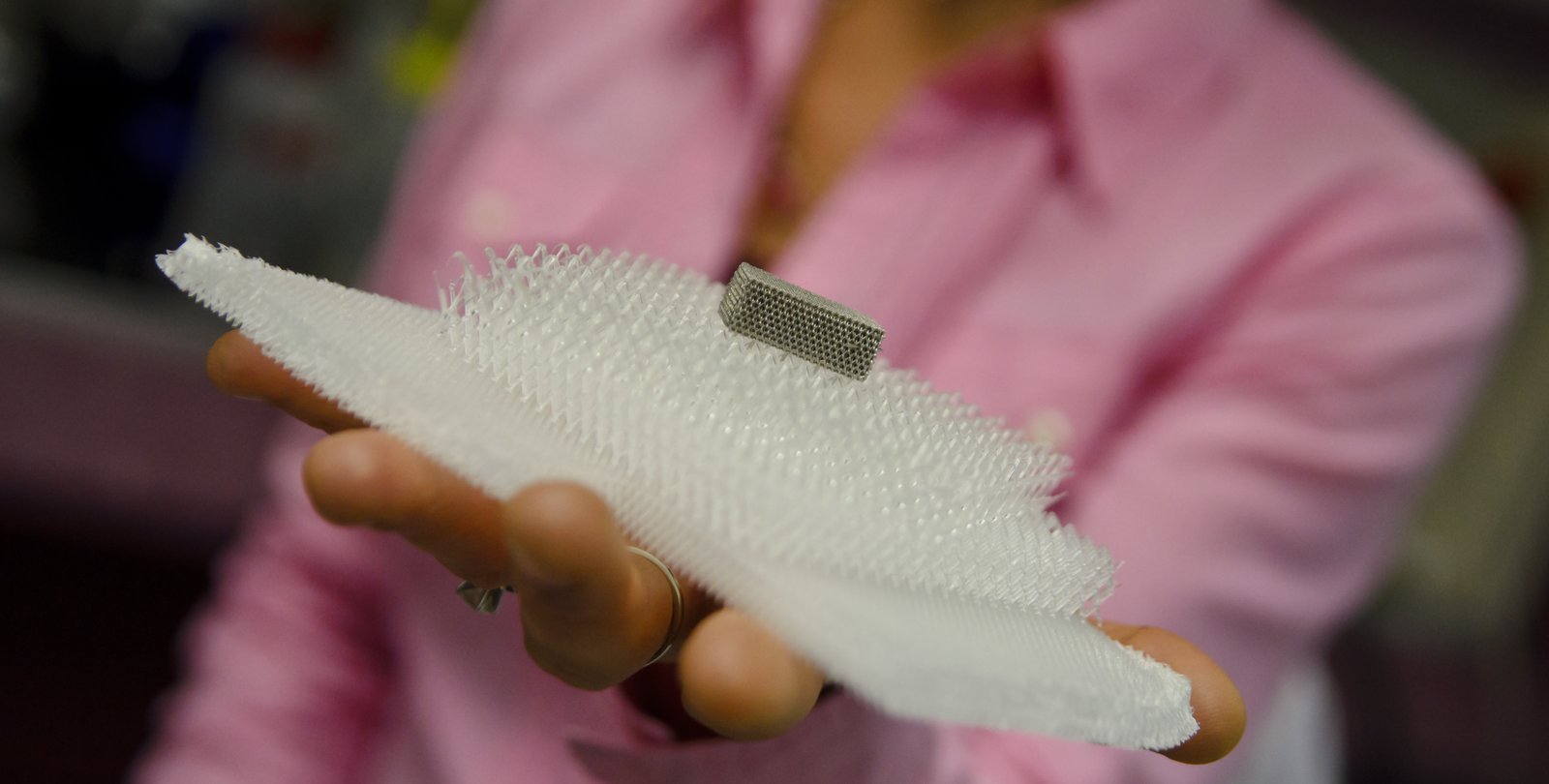
Medicine, Energy, Defense, Space, and Earthquakes: The Far-Reaching Arm of Solid Mechanics Research at Caltech
To better understand the field of solid mechanics as studied at Caltech, ENGenious approached 11 members of the faculty from a variety of disciplines, including aerospace engineering, materials science, mechanical engineering, and geophysics. Solid mechanicians focus on the deformation and failure of materials with a defined rest shape—for example, the solid parts of Earth, the human-built environment, and biological matter such as the human body. An over-arching theme is to study the physics of a solid body's reaction to diverse influences—stress, deformation, temperature changes, electromagnetic fields, fluid flow—and how it fails. This is addressed on a range of length scales, from a cluster of atoms to tectonic plates, using experimental, theoretical, and computational methods. It also involves behaviors happening at highly diverse timescales, from picoseconds all the way to geologic timescales.
Professor Michael Ortiz, who is the first recipient of the prestigious Rodney Hill Prize in Solid Mechanics, describes the Caltech solid mechanics group as covering the "entire waterfront of solid mechanics." He explains, "Solid mechanicians act as a bridge between fundamental science and industry. We at Caltech take a broad view: in a sense, we take the baton all the way to the finish line. We are involved in real-world applications, engineering, and testing. We are needed, and that's why we're still in business."
Ortiz's colleagues describe his seminal contributions to the field as a combination of cutting-edge mechanics and mathematics. He sees himself as primarily an engineer. "Others come to the field from physics or applied math and may have a different emphasis," he explains. "As an engineer, I envision the end application. We start with an application and do whatever we need to solve the problem or make progress in an area—we may use applied mathematics, computational mechanics, or another approach, but our research and our papers are always applications-driven."
Caltech solid mechanics group member Professor Ares J. Rosakis underscores their unique approach. "We have an even balance of theoreticians, experimentalists, and numerical analysts, and we respect this balance, which does not necessarily exist at other universities," he says. "We are very interactive—we mix it up. We do not believe that only theory, only numerics, or only experiments do justice to our field. Of course, we have excellent people and excellent students—but this strong commitment to continuous interaction among group members is what really gives us the edge." In the context of his research, Professor Rosakis adds, "We have been able to do research that other solid mechanics groups have not been able to do because of the combination of very high investment in new experimental techniques and an unusually strong theoretical understanding. That combination and our strength in experimental mechanics have allowed us to move into the area of earthquake source dynamics. We are simultaneously applying an arsenal of diagnostics and theoretical knowledge in dynamic failure of engineering solids to attack the problem of earthquakes." What's next? "I want to pursue ‘laboratory earthquakes' and create my dream: a seismology facility analogous to the Caltech wind tunnel—the seismological wind tunnel!" says Rosakis. "With my academic roots in aerospace engineering, I would use a fluid mechanics approach, in which models are tested in highly instrumented environments with multiple and synchronous diagnostics. A sophisticated seismic testing facility will enable us to observe and measure simulated earthquake events that are difficult, if not impossible, to measure in situ."
Computational solid mechanician and Professor of Mechanical Engineering and Geophysics Nadia Lapusta uses the experiments of Professor Rosakis to inform her earthquake modeling. "My colleagues and I are conducting lab experiments and developing theories to understand the mechanical properties of the earth, which helps us build sophisticated numerical models to explain the observed phenomena," she says. "The next question is whether we can produce a physics-based model that allows us to predict a range of earthquake fault behaviors. We won't predict a specific earthquake event, but we can use our results to offer a range of plausible future events. As we continuously enhance our models based on observations, experiments, and theories, we will eventually succeed in doing this." Professor Lapusta works with other solid mechanicians and geoscientists to understand fault interactions that include the full spectrum of scales—from the macroscopic scale of Earth's crust to the microscopic scale of granular materials (such as soil, decomposed granite, or sand). Micromechanical modeling is essential to her quest to discover the physical law governing earthquakes. "The rapid motion that generates earthquakes occurs in the highly pulverized core of fault zones, within millimeter-wide layers which are composed of nano- to micrometer-sized particles," she says. "If the laws we use are based on a first-principles theory of how these granular materials interact, and that is verified by experiments, then we will have more confidence in applying our models to regimes where experiments cannot be done."
José E. Andrade, Associate Professor of Civil and Mechanical Engineering, further explained the importance of the micromechanical approach. "We're trying to unravel what makes geological materials tick on a large scale. Landslides, earthquakes, or liquefaction can devastate an entire region, but all of these processes are controlled on a minute or granular scale. It's really about a grain in touch with another grain. If we could understand how these grains interact, then we can understand why landslides occur, or how sand castles hold together." Professor Andrade describes his plans to introduce higher standards to his computer models. "We've been forcing our models to adhere to higher standards by comparing them with actual experimental data," he says. "We have developed strong connections with other experimentalists in this area, but I also would like to pursue a suite of boutique-type experiments—that is, conduct clever but uncomplicated experiments that motivate us to pursue a certain line of research, while keeping our models honest." Andrade is also interested in testing his models in space research: "An exciting project we're interested in is using some of our tools for planetary exploration. We'd like to increase our understanding of interactions between spacecraft and regolith (a layer of loose, heterogeneous material covering solid rock on Earth and other celestial bodies) in extraterrestrial conditions."
Many Caltech solid mechanics faculty have strong ties to NASA's Jet Propulsion Laboratory (JPL), the lead U.S. center for robotic exploration of the solar system and the home of major programs in space-based Earth sciences. An especially strong collaboration exists between Caltech and JPL in the form of a dual appointment: Sergio Pellegrino is the Joyce and Kent Kresa Professor of Aeronautics and Professor of Civil Engineering, and Jet Propulsion Laboratory Senior Research Scientist. For Professor Pellegrino, this association has been key. "The pivotal moment was when I decided I would move from Cambridge to Caltech to start my second career," he says. "Caltech is unique. A second career is likely to bring even greater rewards than the first, since one benefits from the experience already gained and one can make better decisions about work going forward: what to do, what not to do. For me, the magical aspect was that GALCIT was reconnecting with space research, and there was and continues to be enormous opportunity to work at the interface between GALCIT and JPL. I have not merely moved to another university and pursued another set of interesting things—I've received strong support and encouragement from the highest administrative levels at both Caltech and JPL."
Professor Pellegrino enjoys working at the intersection of two different fields, which he has done since his student days. "I was interested in working across the gap between engineering and design—especially the analysis of lightweight structures," he says. "I now work across a different kind of gap—between space engineering and solid mechanics. I position myself in the middle and work to either solve an existing problem or to identify problems no one else is thinking about. About ten years ago, for example, I worked on very thin films for structures such as ultralight space-based communication antennas or sunshades to shield telescopes from the sun. When I thought about how curved surfaces in these structures should be designed, I realized that a deeper understanding of the mechanics of wrinkled films was required. A sunshade does not have to be perfectly smooth; if we allow it to become a little bit wrinkled, we can then simplify its design and make it much lighter, but to do this we need a rigorous analysis of how far from perfectly smooth the film will be. This type of analysis had not been done before, as it wasn't recognized to be important. That's an example of how innovation comes about by working at these interfaces—posing a real problem that a designer has, applying the knowledge of the mechanics community, and discovering new solutions."
Innovation and creativity are also at the heart of Professor Chiara Daraio's research. "New materials inspire innovation: When new materials are discovered, new applications, systems, and devices can be invented," she says. "Our group designs materials and devices with new mechanical and acoustic properties. We create materials by selecting simple building blocks that interact in interesting ways, and then we assemble them into more complex structures. The way the building blocks interact with each other determines the overall mechanical properties that characterize the final materials. This is an unconventional approach to the creation of materials that merges the basic principles of solid mechanics with materials science. Working at the interface of such traditionally separate disciplines is easy in Caltech's diverse and broad solid mechanics group. Although the day-to-day focus is on fundamental physics and mechanics, Professor Daraio's experimental work has many applications, including the control of vibrations in space structures, the fabrication of new thermally stable mirrors, and mechanical energy harvesting. But when asked about the future of solid mechanics, she emphasizes biomedical applications. "I believe the design of new materials can have a large impact on biomedical applications. For example, my group uses some of the nonlinear acoustic devices we built to test hard biological systems, such as bones or the stability of implants, through a collaboration with the University of California at Los Angeles Department of Orthopedics. And with our new acoustic lenses, we hope to help build systems that improve ultrasonic imaging and ultrasonic surgery."
Biomedical applications and experimental mechanics have been an element of Caltech solid mechanics research for most of the time Professor Emeritus Wolfgang Knauss has been at Caltech. "I believe the strong adherence to experimental work makes us unique," Professor Knauss says of the Caltech solid mechanics group. "Until about 10 to 15 years ago, the GALCIT solid mechanics group was virtually all experimentally based. There are so few experimentalists in the world, in particular in the United States. But Caltech is strong in that regard. Many people essentially wait for experimental results so they can go on with the theory; I think that's where our strength has been, and I hope we don't lose that in spite of the more recent addition of a formidable numerical analysis component."
With regard to biomedical applications, Knauss recalls his research 30 years ago with the Doheny Eye Institute at the University of Southern California (USC). "Before there was laser treatment for nearsightedness, a surgical procedure called radial keratotomy was used to correct myopia," he explains. "Surgeons made little radial cuts in the cornea of the eye, and by carefully placing the cuts, controlling the depth and number of cuts, they could correct acuity. A Russian doctor, Svyatoslav Fyodorov, invented this procedure in 1974, when a 17-year-old accident victim came to him with eyes that had been lacerated by glass shrapnel. When the eyes healed, the patient had better vision than before. Fyodorov postulated that the central portion of the lens is curved outward because of a ligament around that part that constricts it and bends it outward. If that ligament is cut, it flattens or changes the lens shape. So the USC doctors consulted with me as a mechanician because they could not find the ligament. But to me it was clearly a fracture problem! You're introducing cracks in a specific material, and when there are cracks coupled with pressure (of the eye), the geometry changes. One of the problems we tackled was that long after healing had occurred, the eye wasn't the same as on the day when the surgeons made the cuts, so we tried to understand how to compensate for that, to make the operation last longer."
Another application of Professor Knauss's research on time-dependent mechanical processes relates to nuclear power plant safety. He explains, "One other area that is close to my heart besides the fracture of viscoelastic polymers is high-speed crack propagation. There were some real issues relating to that in the late 1970s to early 1980s, when nuclear power plant safety was a highly rated issue. Funding was available to develop theories and frameworks to enable prediction of how reactors could break up if they were suddenly cooled. When something goes wrong in a reactor, it is flushed with water, which quenches everything and, in turn, causes tremendous thermal stresses. What we tried to understand was how fast the cracks could propagate, and determine the possible consequences. In that process, we were able to explain the discrepancy between the theoretical estimate and the measured maximal crack speed attained, the theoretical value being typically about twice the measured values."
Many solid mechanics research applications are transforming our world and benefiting society, but new applications and discoveries rely on fundamental knowledge. Professor Guruswami (Ravi) Ravichandran explains, "Our research in solid mechanics is focused on engineering science problems. We are not working on today's relevant systems or technologies, but we are working on mechanics problems that will impact future technologies. For example, I apply rigorous mechanics to the study of cell mechanics and interaction with biomaterials. Most cell experiments are performed on glass slides, on two-dimensional substrates, but that's not really a physiologically relevant environment for the cells. Cells are living in a three-dimensional world, so we explore the mechanics of cells in 3-D. We want to know the mechanical forces involved in cell division, because doing so can lead to a better understanding of the physiological processes involved in tissue engineering. We need to know the mechanical properties of the extracellular matrix in artificial tissues or organs. As scientists try to grow organs, they will need to know what forces are involved, and how to best mechanically match compliance of the cells with elasticity of the matrix. If there is a mismatch, for example, in creating artificial vessels for grafts, the grafts could be too stiff, and the cells are not going to like that. One must have the right match between the mechanical properties of the extracellular matrix and the cells, so the cells can properly function."
Professor Ravichandran is also studying how materials deform or change shape at different scales and temperatures when struck by a high-speed projectile. This work is of special interest to the U.S. Army Research Laboratory, which is funding a $90 million initiative to improve protective gear and vehicles for soldiers. Several members of the Caltech solid mechanics team will be working on this initiative, including Julia R. Greer, Assistant Professor of Materials Science and Mechanics. "I think this initiative is going to represent a big thrust in solid mechanics—in part because it is work by experimentalists such as Ravichandran and I in collaboration with computationalists, like Dennis Kochmann and Michael Ortiz," she says.
Professor Greer describes her research in the context of the Army initiative this way: "To understand the physics and the mechanics of materials deformation, we want to know what's happening at the atomistic level, because materials don't behave in the same way when they're very small. We bring a little fresh air into the atmosphere of classical laws, which break down at the nanoscale. I'm in ‘nanosolid' mechanics, and I've been studying the behavior and response of nanosolids to mechanical deformation and investigating what within their microstructure gives rise to their unique properties, which are different from those of the same solids but with large dimensions. We are finally at a place where we have a pretty good understanding of the fundamental mechanical behavior and want to use these nanosolids as building blocks to construct tangible materials. The idea is to capitalize on the very unique properties that are offered by nanomaterials to create hierarchical structures, such as three-dimensional lattices, or scaffolds. For example, we have built microtrusses, which were recognized as the world's lightest material and could sit on top of a white-top dandelion without perturbing it. We are now building nanotrusses, where every dimension is less than a couple of microns, so you can't see the structure with your eye. With the microtruss, you can see very clearly that it's a structure and can say, ‘Oh, this is a bunch of octahedrals sitting on top of each other.' But when you make every dimension below a micron, your eyes can't resolve the structure and so it looks like a cloud just sitting in your hand—it's very cool! To actually make these nanosolids into useful materials and structures, we have to figure out how to cheaply and effectively manufacture materials that have nano-constituents."
The newest member of the solid mechanics group, Dennis Kochmann, Assistant Professor of Aerospace, shares Professor Greer's passion for creating materials from the nanoscale up. He explains, "It all comes down to: How do you carefully design a material's microstructure so that you get whatever macroscopic properties you want? You start at the lower scales, e.g., by combining several existing materials into a new artificially designed composite material, and one thereby normally combines materials that have desirable individual properties, such as one that is very strong and stiff and one that dampens vibrations by absorbing energy. (These two properties are generally exclusive in nature, and therefore materials that combine both properties are of urgent need in engineering applications.) As part of our research, we study composites that include active or tunable materials that respond to external stimuli such as temperature or electric fields. This way, you can create new materials whose properties are tunable over wide ranges by applying the appropriate external stimulus (e.g., changing the temperature, applying an electric voltage, etc.). Doing so will trigger mechanisms on the microscale, which give rise to significant change in the macroscopic properties." He goes on to describe his long-term research vision: "I hope to extensively explore this idea in the experimental lab and computationally. Our everyday engineering applications always require materials that are harder, stiffer, stronger, lighter, more resistant and durable. Someday, we would like to be able to switch the properties of artificial materials to exactly what is needed. We want to be able to design future materials on demand."
Professor Kaushik Bhattacharya expands on this idea. "The scales at which we are beginning to do engineering are merging, and the great challenges in solid mechanics are giving rise to a language that bridges materials science and mechanical engineering," he says. "Today, we teach our mechanical engineering undergraduates how to manipulate the properties of materials to engineer large structures. Now we also look at microstructures, and the toolbox with which we control structure is dramatically changing. It's no longer about beating, heating, or cutting a blob of metal. It is much more complex today. Our challenge is not to shape the material to get the function we want, but how we create a specific material that already possesses the function we want. We are in fact merging both material and machine—and that is absolutely exciting!"
Professor Bhattacharya's excitement is shared by a strong and active student group that organizes a yearly solid mechanics symposium in celebration of the late James K. Knowles, Caltech's William J. Keenan Jr. Professor of Applied Mechanics, Emeritus. Professor Knowles made fundamental research contributions to the mathematical theories of materials and structures. He was a special teacher and mentor who inspired and influenced multiple generations of students and scholars through classes in mathematics and mechanics. Continuing this visionary thinker's contributions to solid mechanics and encouragement of young researchers are his junior colleagues, who continue to take Caltech's solid mechanics research in innovative, interesting, and new directions. "Jim was the greatest mentor I ever had," says Professor Rosakis. "He held my hand when I first came to Caltech as an assistant professor. He also taught me how to teach. He would look for the spark in people's eyes and help them make their dreams a reality. As we at Caltech seek to create the best mentoring opportunities for our young faculty, we are guided by his example."